top of page
Coatings
Our products are simply the delta in the performance of your devices versus uncoated—pure value.

Hydrophobic Coatings
Apply hydrophobic nonstick coatings to prevent tissue adhesion; to facilitate the release of molded parts; or to improve fluid dispensing and prevent carryover in pipette tips, needles, and probes. Apply hydrophobic barrier coatings to protect electronic components.
Hydrophobic coatings decrease surface energy and wettability.
Hydrophobic coatings have a water contact angle between 90° and 150°.
Superhydrophobic coatings have a water contact angle ≥ 150°.
Oleophobic coatings are also possible, as are coatings that are both hydrophobic and oleophobic.
Hydrophobic coatings decrease surface energy and wettability.
Hydrophobic coatings have a water contact angle between 90° and 150°.
Superhydrophobic coatings have a water contact angle ≥ 150°.
Oleophobic coatings are also possible, as are coatings that are both hydrophobic and oleophobic.

Lubricious Coatings
Apply lubricious coatings to lower the force needed to insert, maneuver, position, and remove minimally invasive surgical devices, such as guidewires and catheters; make it easier and safer to reach difficult lesions and pass through tight stenoses; enable improved tracking; facilitate more precise placement of implants; and reduce trauma. Because less force is required, the devices can be used with greater and more predictable control, accuracy, and safety.
By lowering the coefficient of friction, lubricious coatings improve the performance of medical devices that involve components that slide across human tissue or against each other. Less friction means less damage to blood vessels and other tissues and makes interactions between device components smoother and more reliable.
Lubricious coatings come in two flavors, hydrophilic and hydrophobic, each with many use cases. Hydrophilic coatings provide wet film lubrication, and hydrophobic coatings provide dry film lubrication. Hydrophilic coatings are generally more lubricious than hydrophobic coatings, but hydrophilic coatings must be wetted before use.
PECVD-applied lubricious hydrophobic coatings are extremely thin, which allows for sturdier devices within the available space, because the coating does not take up much room, allowing larger components to be used.
By lowering the coefficient of friction, lubricious coatings improve the performance of medical devices that involve components that slide across human tissue or against each other. Less friction means less damage to blood vessels and other tissues and makes interactions between device components smoother and more reliable.
Lubricious coatings come in two flavors, hydrophilic and hydrophobic, each with many use cases. Hydrophilic coatings provide wet film lubrication, and hydrophobic coatings provide dry film lubrication. Hydrophilic coatings are generally more lubricious than hydrophobic coatings, but hydrophilic coatings must be wetted before use.
PECVD-applied lubricious hydrophobic coatings are extremely thin, which allows for sturdier devices within the available space, because the coating does not take up much room, allowing larger components to be used.
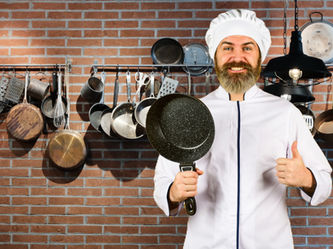
Nonstick Coatings
Apply nonstick coatings to mandrels used to manufacture catheters (extrusion, reflow, forming, bonding, welding, tipping, inspection); to the ID and OD of needles, probes, and pipette tips for more precise dispensing and to prevent carryover; to electrosurgical cutting and sealing devices so that they operate optimally with minimal eschar buildup; and to molds for improved release.

Antimicrobial Coatings

nano-thin coatings
Our ultrathin coatings take up only a tiny amount of space, but the performance enhancement for your device can be massive. Is something like 70 nanometers your sweet spot? Need ± 7 nm to go with that? That can be done. One of our core strengths is to precisely control the film thickness of ultrathin coatings.
Plasma-enhanced chemical vapor deposition (PECVD) enables coatings to be applied extremely thin, which helps manufacturers design smaller medical devices as part of the move to device miniaturization.
Or, because nano-thin coatings take up very little space, they can leave room for additional device components or for larger device components. For example, if a wire is coated with a nano-thin PECVD coating instead of with a relatively thick PTFE coating, a heavier wire can be used within any given space constraint. This is important because a heavier gauge wire will be a significantly stronger, safer, and more robust device component. (According to Guidewires: The Basics, https://www.youtube.com/watch?v=Peu8_GL3m0I&t=403s, at 6:43, the strength of a guidewire is related to the radius to the fourth power, which means that a 0.018” guidewire is 2.73 times stronger than a 0.014” guidewire.)
Ultrathin coatings also add very little mass to miniature components.
We apply coatings with thicknesses anywhere from 50 nanometers up to 3 microns, based on customer requirements. Thicker coatings are possible, when we apply, say, a liquid hydrophilic topcoat over a PECVD-applied linker.
Plasma-enhanced chemical vapor deposition (PECVD) enables coatings to be applied extremely thin, which helps manufacturers design smaller medical devices as part of the move to device miniaturization.
Or, because nano-thin coatings take up very little space, they can leave room for additional device components or for larger device components. For example, if a wire is coated with a nano-thin PECVD coating instead of with a relatively thick PTFE coating, a heavier wire can be used within any given space constraint. This is important because a heavier gauge wire will be a significantly stronger, safer, and more robust device component. (According to Guidewires: The Basics, https://www.youtube.com/watch?v=Peu8_GL3m0I&t=403s, at 6:43, the strength of a guidewire is related to the radius to the fourth power, which means that a 0.018” guidewire is 2.73 times stronger than a 0.014” guidewire.)
Ultrathin coatings also add very little mass to miniature components.
We apply coatings with thicknesses anywhere from 50 nanometers up to 3 microns, based on customer requirements. Thicker coatings are possible, when we apply, say, a liquid hydrophilic topcoat over a PECVD-applied linker.
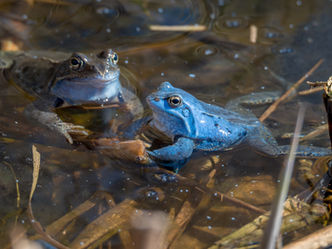
Hydrophilic Coatings
Plasma-treat plastics to make them hydrophilic. Apply hydrophilic coatings to medical device components to dramatically increase lubricity.
Hydrophilic coatings increase surface energy and wettability.
Hydrophilic coatings have a water contact angle between 10° and 60°.
Superhydrophilic coatings have a water contact angle < 10°.
Hydrophilic coatings increase surface energy and wettability.
Hydrophilic coatings have a water contact angle between 10° and 60°.
Superhydrophilic coatings have a water contact angle < 10°.

ID Coatings
Apply coatings to the inner diameter (ID) of hypotubes, laser-cut hypotubes, coils, HHS® tubes, and torque tubes to make them lubricious or nonstick; to the ID and OD of needles, probes, and pipette tips for more precise dispensing and to prevent carryover; and to the insides of vials, microplate wells, test tubes, centrifuge tubes, and PCR tubes to make them hydrophilic, prevent leaching, or to apply a functional coating.

Functional Coatings

Barrier Coatings
Apply ultra-thin conformal barrier coatings to printed circuit board assemblies for chemical, moisture, and dielectric barrier protection; to components in wearables, such as watches and hearing aids, to make them sweatproof, splash-proof, or waterproof; to IVD laboratory and pharmaceutical containers to prevent leaching and gas permeation.
bottom of page