
Inspired by Nature.
Lotus Leaf
The lotus leaf effect is a well-known bioinspiration for hydrophobic surface modification.
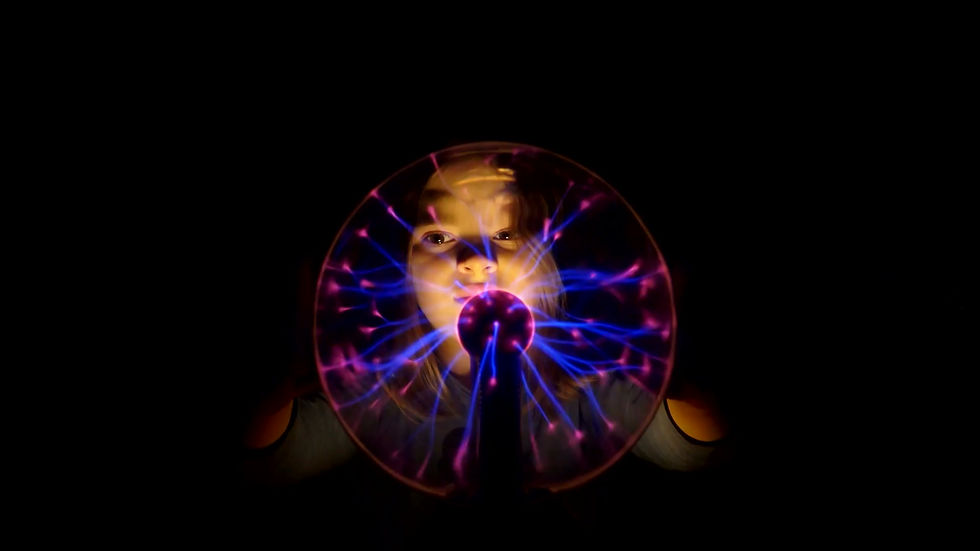
Empowered by Science.
Interacting with a Plasma Globe
Plasma science enables many wondrous surface modifications.

To Improve Health.
Health Brings Joy
We're with you. We know why you do what you do, and it's the same reason we do what we do.
Interlayer is a California-based custom coating company. We provide advanced surface modification for medical devices and laboratory consumables.
​
Taking inspiration from nature, with an emphasis on how the human body overcomes challenges related to friction, sticking, and defense against microbes, we apply rigorous scientific methodology to create advanced surface chemistries and morphologies on medical device components and IVD laboratory consumables.
​
We take a flexible, adaptable approach to working with customers to optimize the surfaces of medical devices to impart desired properties. We supply everything necessary for successful coating development and production projects, including coating development, equipment, consumables, production design, installation, training, knowledge transfer, preventative maintenance, and technical support. We also offer consulting and contract coating services.
​
We create significant value for our customers: by doing things that no one else can do and by transforming low-value inputs into high-value outputs.
​
For example, we might help an injection molder transform a $2 part into a $50 part by applying a functional coating.
​
We work with medtech R&D teams to overcome challenges related to friction, sticking, microbe control, robustness, testing, miniaturization, and more. We also work with them to push the boundaries of medical technology by jointly optimizing the properties of the bulk materials and surfaces of device components.
​
For example, by using an extraordinarily thin, lubricious coating on a wire component, a heavier gauge wire can be used, which can improve the strength, robustness, and risk profile of the device.
​
We work with IVD companies to improve laboratory consumables by tailoring their surfaces for the intended application. This often involves applying a coating to make a plastic surface hydrophilic, which can help improve the signal-to-noise-ratio of the associated diagnostic test.
​
Because the incorporation of advance coating technologies into medical devices can often lead to major performance improvements (or are outright enabling), we encourage our customers to leverage our coating expertise to help them:
-
improve existing product lines
-
increase margins
-
gain market share
-
increase a competitive advantage (widen an economic moat)
-
introduce next-generation products
-
introduce entirely new classes of products
Interlayer was founded to create value for customers and patients via comprehensive surface modification solutions:
-
To tame the complexity of surface modification solutions to make them useful for customers. If surface modification were easy, you could just buy most things off the shelf. But it’s not always easy. That’s what we are here for.
-
To overcome the limitations of outdated business plans that require customers to stitch together partial solutions from a tangle of vendors that are each variously focused on selling equipment, coating materials, consulting services, R&D, or contract processing. We get that time and budget constraints require a better way of doing things. We do what you want, not what we want.
-
To expand the use of plasma-enhanced chemical vapor deposition (PECVD) to customers who might not know how precise, reproducible, and cost-effective it is as a method of chemical synthesis. Often, PECVD is the most efficient way to apply a coating. It's rewarding to use relatively few resources yet have a large effect on the standard of living for so many people.
-
To design cost-effective processes that help device manufacturers capture a high percentage of the value they create, instead of squandering much of it on expensive production processes.
-
To promote a culture of looking for even better. (We like a chess analogy for this: Emanuel Lasker, who was World Chess Champion for 27 years, famously said, “When you see a good move, look for a better one.”)
-
To push the scientific boundaries of what is possible as the world demands ever-smaller, more precise, and reliable medical devices and in vitro diagnostic tests. Academics coat stuff all the time. Part of what we do is translate what might be complex and/or expensive in an academic lab into something that is practical and cost-effective in the real world.
-
To sift through the multitude of surfaces provided by nature and find those that can be mimicked on synthetic materials to make them play well with humans. Of course, humans come up with a lot of great ideas on their own, and we use those too.
-
To never again have to say, “You’re how deep into this project, and you’re just now reaching out to me? It’s going to be expensive to fix this.”